1)組合夾具虛擬設計實例
具體應用步驟有:
①以零件實體模型作為設計依據(jù)
②按設計需要選用支撐組件、壓緊組件、基礎組件、定位組件、導向組件等元件、組件。
*元件、組件不帶知識庫的可以從標準件、組件樹上直接下載。
*元件、組件帶知識庫的,通過組件設計推理,進行組件、元件的推理和系列尺寸驅動,并下載到工作區(qū),進行裝配。
③組件和元件之間的裝配。對于已經(jīng)下載的各類元件和組件,使用三維CAD平臺裝配功能進行裝配,并輸出結果,完成整個組合夾具的設計。組合夾具其裝配示例見圖12-22,SolidWrorks平臺下的增強裝配實例見圖12-23.
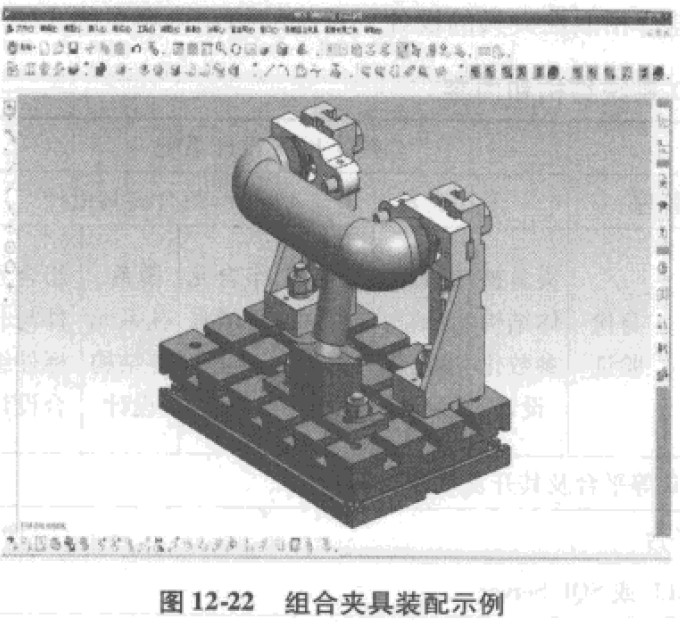
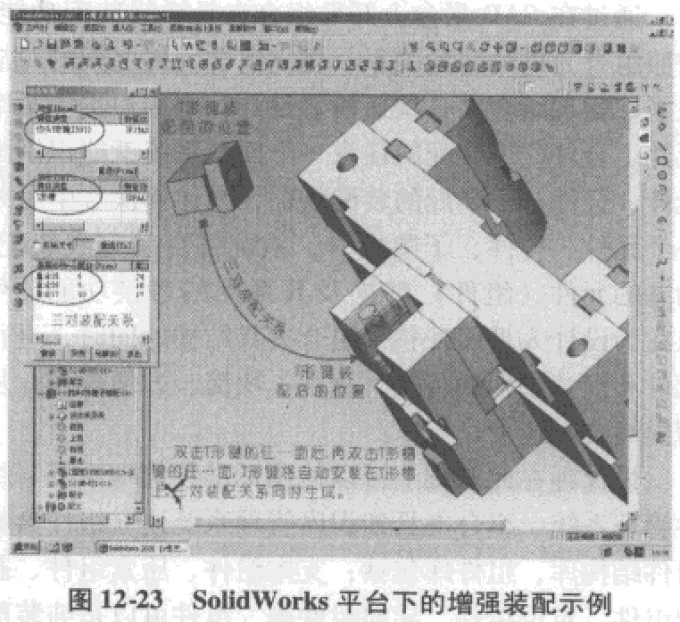
2)專用夾具設計實例
具體設計步驟
①根據(jù)被加工零件的尺寸參數(shù)及其形狀,在基礎版庫中選擇可用基礎版或進行基礎版建模;連桿被加工零件見圖12-24,基礎版見圖12-25.
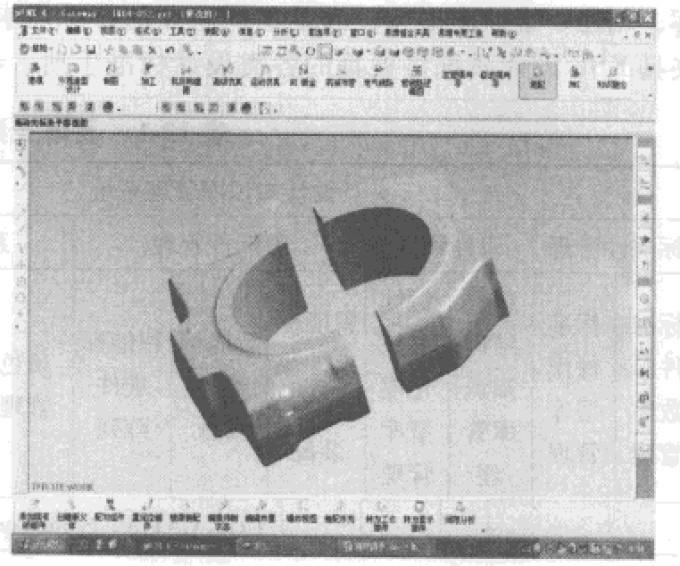
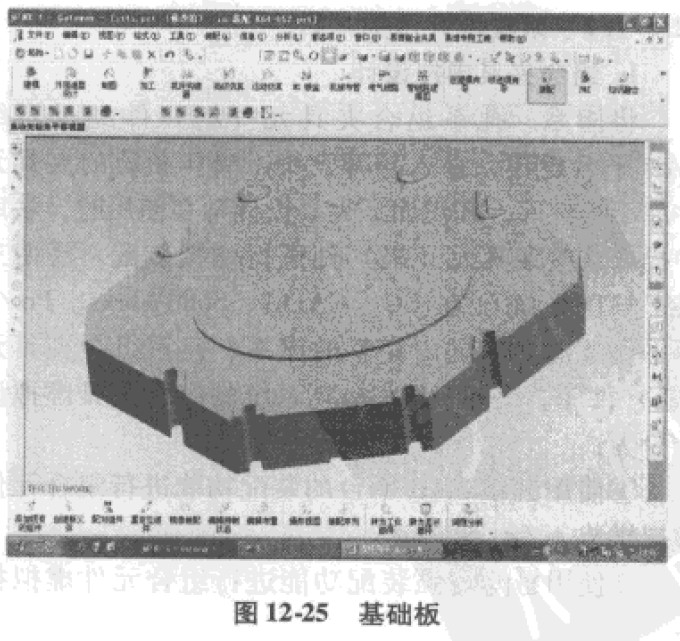
②智能件打孔裝配加快專用夾其設計。將標準件緊固螺釘、定位銷、螺栓、檔銷等制作成具有裝配屬性的智能件,這些智能件具有打孔、裝配一次性完成功能,并可實現(xiàn)多層板的打孔及各層板的間隙設置。定位銷智能件在打孔裝配操作后,還具有陣列、刪除、修改等功能,如若智能件規(guī)格不臺適,還可直接進行足寸系列替換,大大提高了專用夾具的工作效率。擋銷智能件見圖12-26,智能件打孔裝配及陣列見圖12-27。
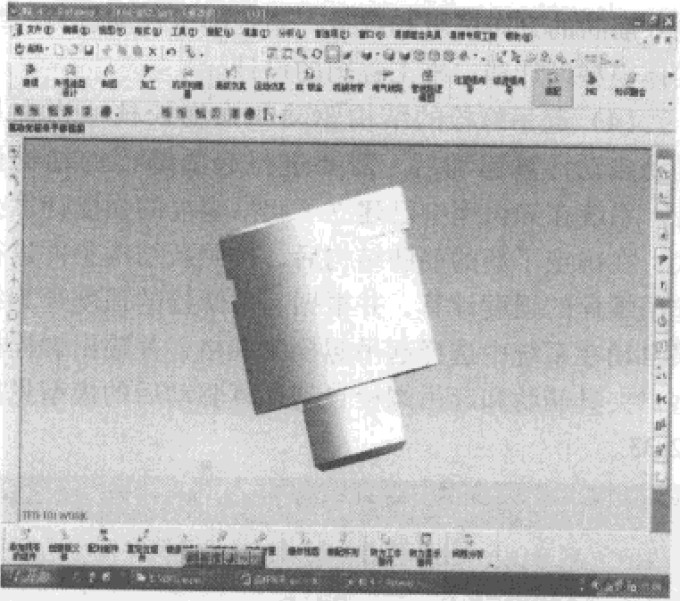
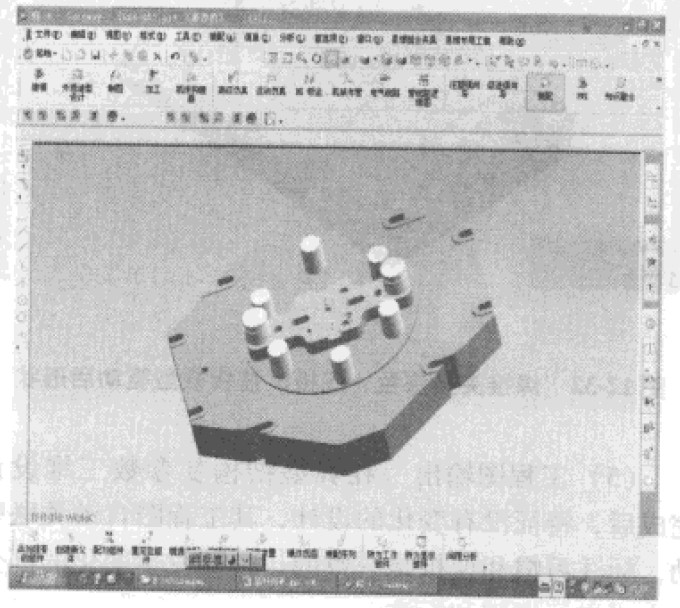
③組件知識庫推理及打孔裝配。建立夾具組件知識庫和智能件,通過采集相關信息,對組件進行知識庫參數(shù)化驅動,并實現(xiàn)組件打孔裝配,陣列,提高組件設計效率。壓板組件打孔快速裝配見圖12-28,壓板組件打孔陣列見圖12-29。
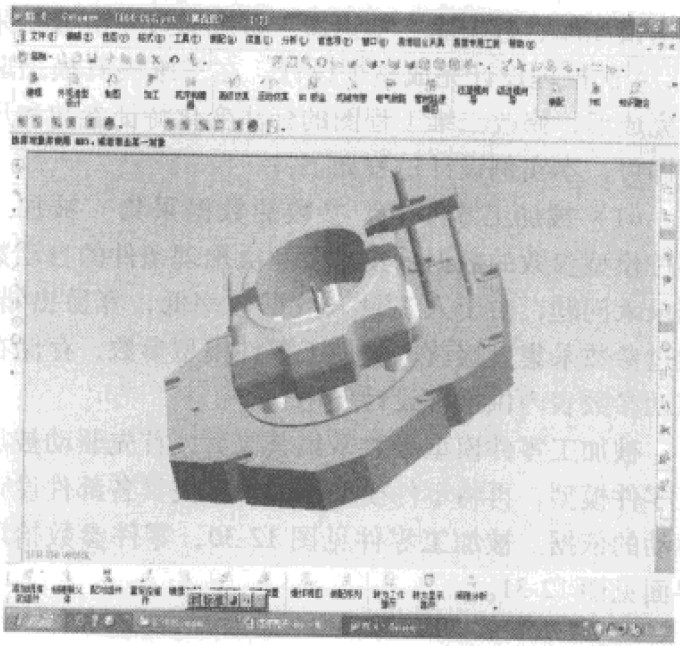
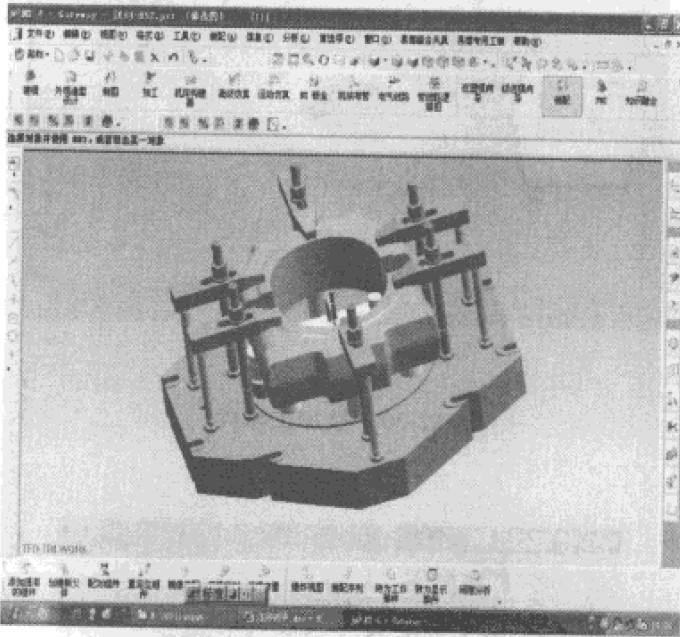
3)夾具典型整體結構設計實例
當夾具具有整體結構重用價值時,系統(tǒng)通過建立夾具典型整體結構參數(shù)化模型庫、知識庫,實現(xiàn)夾具變結構快速設計,在設計環(huán)節(jié)中如果遇到一些強度計算問題,在建立知識庫推理時可以將相應的公式計算(含有限元分析計算結果)整理入庫,當再次使用時通過系統(tǒng)進行推理計算以滿足快速設計的需要。以下結合某廠焊接夾具設計為例,簡述典型整體結構設計過程。通過前期對焊接夾具典型結構的實體模型、設計經(jīng)驗、計算公式、二維工程圖等數(shù)據(jù)、圖形的總結整理后.已經(jīng)建立該類零件的焊接夾具典型結構模型庫、數(shù)據(jù)庫、知識庫。系統(tǒng)通過4次數(shù)據(jù)采集,4次推理設計完成整個設計。在三維夾具模型驅動完成后,修改二維工程圖的標注變化特征參數(shù)和尺寸即可。
本實例設計過程如下:
①被加工零件模型參數(shù)的數(shù)據(jù)采集被加工零件模型參數(shù)的數(shù)據(jù)采集主要解決推理條件的自動數(shù)據(jù)錄入問題,由于人工錄人數(shù)據(jù)效率低,容易出錯。通過參數(shù)采集直接獲取被加工零件模型參數(shù),存儲在驅動參數(shù)表內供推理設計使用。被加工零件模型參數(shù)采集獲取后,首先驅動被加工零件模型,再將零件模型作為焊接夾具各部件設計驅動的依據(jù)。被加工零件見圖l2-30,零件參數(shù)拾取界面見圖12-31。
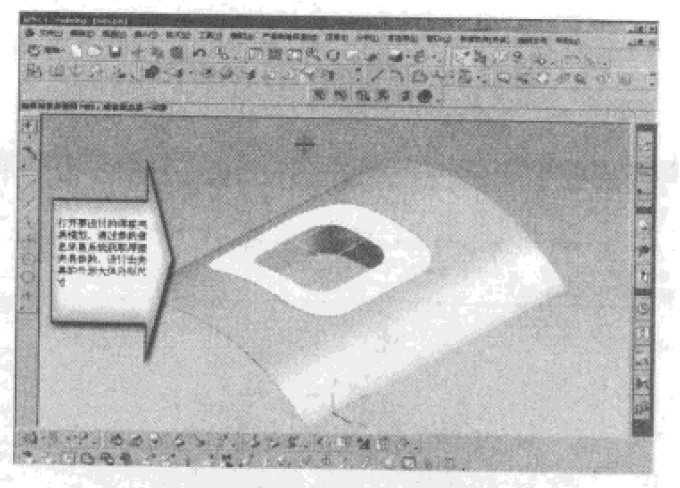
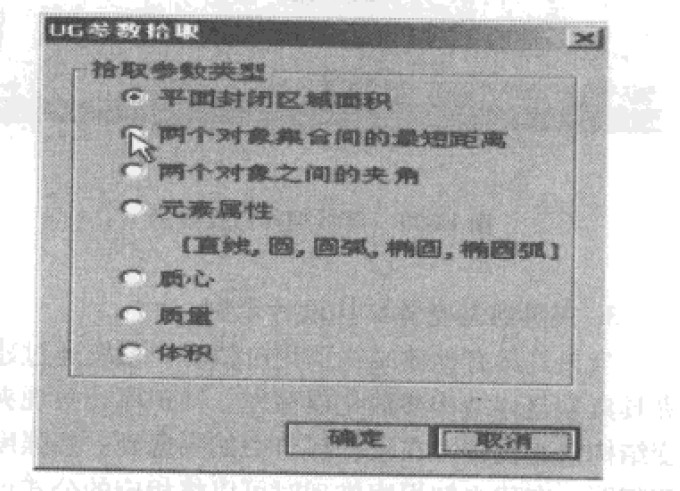
②驅動法蘭、底板、蓋板零件模型由被加工零件模型的驅動結果作為焊接夾具法蘭、底板、蓋極零件模型驅動條件,在知識庫中自動進行推理驅動,焊接夾具法蘭,底板、蓋板模型驅動后形狀見圖12-32
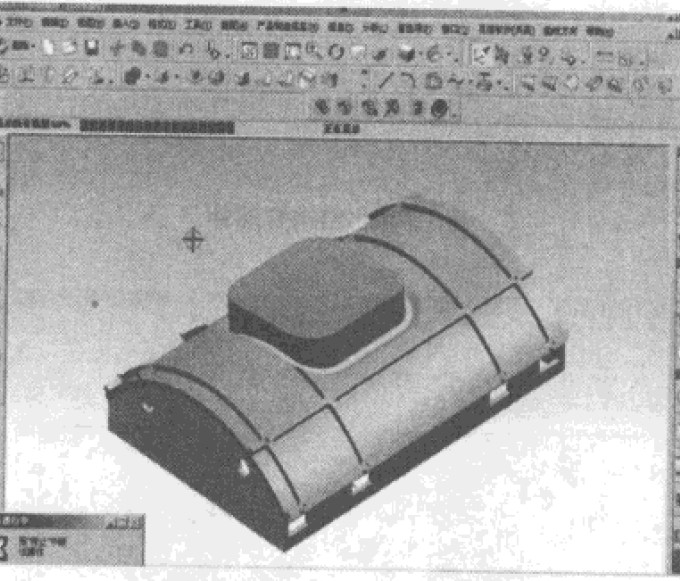
③筋肋自動計算驅動
焊接夾具的筋肋設計是一項非常繁瑣的設計工作,設計員需要反復計算、畫圖,如果一次計算不合理或因其它原因變化還需反復修改,工作量大。本設計在知識庫中建立了推理規(guī)則,將筋肋設計經(jīng)驗和算法存入知識庫,設計時只需輸入筋肋的分布區(qū)域和數(shù)量,系統(tǒng)即可自動進行三維實體模型設計和二維工程圖的設計。
④起吊螺栓的結構驅動和強度校核
當夾具筋肋自動計算驅動后,需要進行起吊螺栓的結構設計。系統(tǒng)在知識庫中已建立了起吊螺栓的強度計算公式,在確定了新的筋肋結構后,按照新結構條件進行起吊螺栓的強度計算,并根據(jù)起吊螺栓的強度計算結果自動在系統(tǒng)中選擇起吊螺栓的規(guī)格,井輸出螺栓模
型.夾具筋肋和起吊螺栓自動計算驕動后的模型見圖12-33。
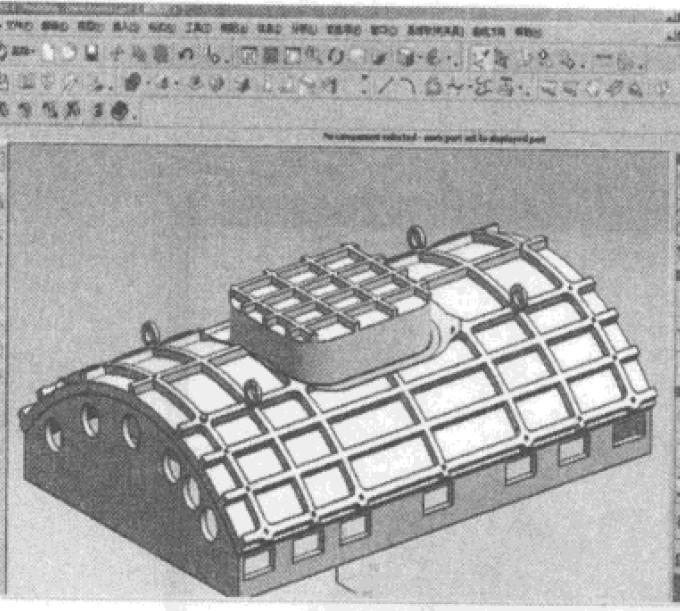
⑤工程圖輸出
在典型結構變參數(shù)三維設計完成后,特征沒有變化的設計,其工程圖自動關聯(lián)驅動,標注習慣和模板是一致的,特征發(fā)生變化的部分由人工進行調整和標注。
鉆夾具的設計實例
圖2-2-20所示為杠桿類零件圖樣。圖2-2-21所示為本零件工序圖。
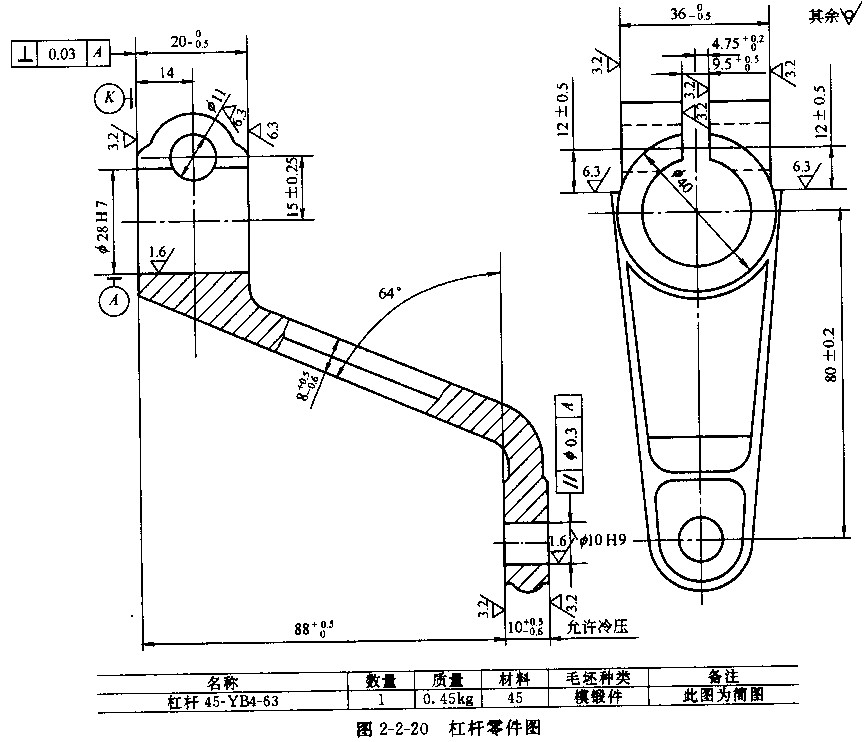
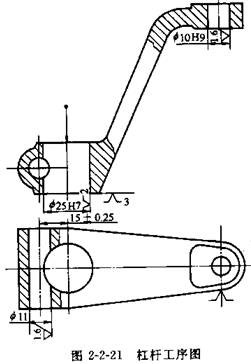
1.零件本工序的加工要求分析
①鉆、擴、鉸φ10H9孔及φ11孔。
②φ10H9孔與φ28H7孔的距離為(80±0. 2)mm;平行度為0.3mm。
③φ11孔與φ28H7孔的距離為(15±0. 25)mm。
④φ11孔與端面K距離為14mm。
本工序前已加工的表面如下。
①φ28H7孔及兩端面。
②φ10H9兩端面。
2.確定夾具類型
本工序所加工兩孔(φ10H9和φ11),位于互成90°的兩平面內,孔徑不大,工件質量較小、輪廓尺寸以及生產(chǎn)量不是很大,因此采用翻轉式鉆模。
3.擬定定位方案和選擇定位元件
(1)定位方案。根據(jù)工件結構特點,其定位方案如下。
①以φ28H7孔及一組合面(端面K和φ10H9一端面組合而成)為定位面,以φ10H9孔端外緣毛坯面一側為防轉定位面,限制六個自由度。這一定位方案,由于尺寸 mm公差大,定位不可靠,會引起較大的定位誤差。如圖2-2-22(a)所示。
②以孔φ28H7孔及端面K定位,以φ11孔外緣毛坯一側為防轉定位面,限制工件六個自由度。為增加剛性,在φ10H9的端面增設一輔助支承,如圖2-2-22 (b)所示。
比較上述兩種定位方案,初步確定選用圖2-2-22(b)所示的方案。
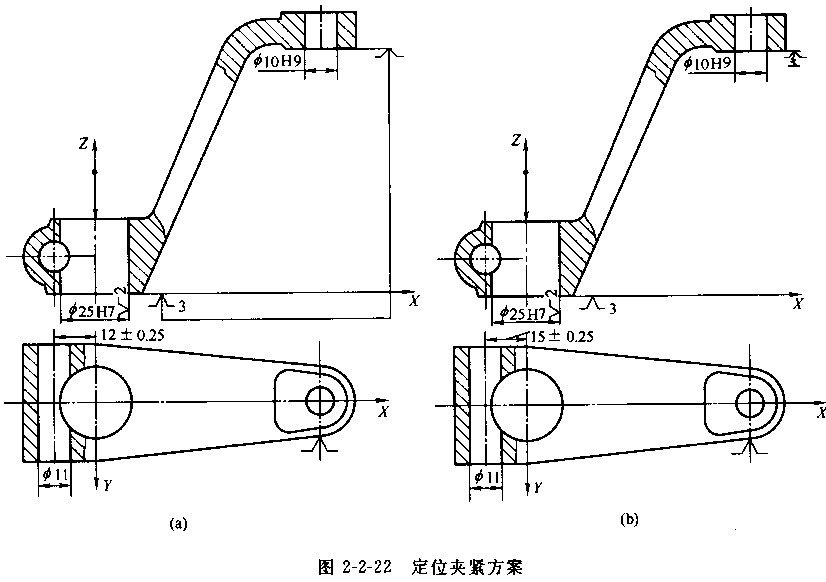
(2)選擇定位元件。
①選擇帶臺階面的定位銷,作為以φ28H7孔及其端面的定位元件,如圖2-2-23所示。定位副配合取 。
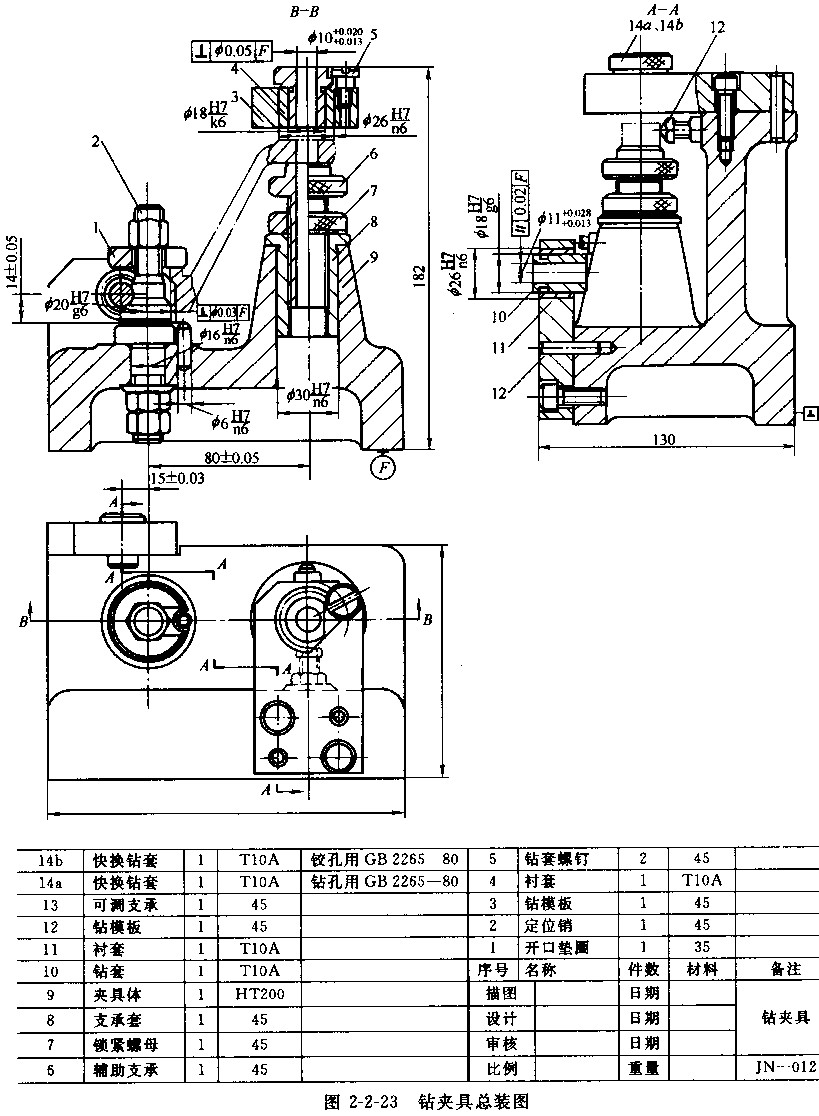
②選擇可調支承釘為φ11孔外緣毛坯一側防轉定位面的定位元件,如圖2-2-24(a)所示。也可選擇如圖2-2-24 (b)所示移動V形塊。考慮結構簡單,現(xiàn)選用圖2-2-24(a)所示結構。
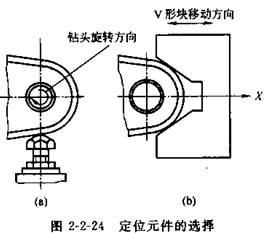
(3)定位誤差計算
①加工φ10H9孔時孔距尺寸(80±0.2)mm的定位誤差計算。
由于基準重合,故ΔB=0。
基準位移誤差為定位孔(φ38 mm)與定位銷(φ38 mm)的最大間隙,故ΔY=(0.021+0. 007+0.013)mm=0.041rnm。
由此可知此定位方案能滿足尺寸(80±0.2)mm的定位要求。
②加工φ10H9孔時軸線平行度0.3mm的定位誤差計算。
由于基準重合,故ΔB=0。
基準位移誤差是定位孔φ28H7與定位面K間的垂直度誤差。故ΔY=0. 03mm。
此方案能滿足平行度0. 3mm的定位要求。
③加工φ11孔時孔距尺寸(15±0.25)mm。加工φ11孔時與加工φ10H9孔時相同。
此方案能滿足孔距(15±0.25) mm的定位要求。
4.確定夾緊方案
參考夾具資料,采用M12螺桿在φ28H7孔上端面夾緊工件。
5.確定引導元件(鉆套的類型及結構尺寸)
⑴對φH9孔,為適應鉆、鉸選用快換鉆套。
主要尺寸由《機床夾具零、部件》國家標準GB/T2263-80, GB/T2265-80選取。鉆孔時鉆套內徑φ10 mm、外徑φ15 mm;襯套內徑φ15 mm,襯套外徑φ22 mm。鉆套端面至加工面的距離取8mm。
麻花鉆選用φ9. 8 mm。
(2)對φ11孔,鉆套采用快換鉆套。鉆孔時鉆套內徑φ11 mm、外徑φ18 mm,襯套內徑φ18 mm,外徑φ26 mm;鉆套端面至加工面間的距離取12mm。
麻花鉆選用φ10. 8 mm。
各引導元件至定位元件間的位置尺寸分別為(15±0.03)mm和(18±0. 05)mm,各鉆套軸線對基面的直線度允差為0.02mm。
6.夾具精度分析與計算
由圖2-2-22可知,所設計夾具需保證的加工要求有:尺寸(15±0.25)mm;尺寸(80±0.2)mm;尺寸14mm及φ10H9孔和φ28H7孔軸線間平行度允差0.3mm等四項。除尺寸14mm,因精度要求較低不必進行驗算外,其余三項精度分別驗算如下。
(1)尺寸(80±0.2)mm的精度校核。
定位誤差ΔD,由前已計算,已知Δ=0.041mm。
定位元件對底面的垂直度誤差ΔA=0.03mm。
鉆套與襯套間的最大配合間隙ΔT1=0. 033mm。
襯套孔的距離公差ΔT2=0.1mm。
麻花鉆與鉆套內孔的間隙X2=0.050mm。
襯套軸線對底面(F)的垂直度誤差ΔT3=0. 05mm。
因而該夾具能保證尺寸(80±0. 2)mm的加工要求。
(2)尺寸(15±0. 25)mm的精度校核。
ΔD=0. 041mm,ΔA=0. 03mm,ΔT1=0. 033mm。
襯套孔與定位元件的距離誤差ΔT2=0.06mm。
麻花鉆與鉆套內孔的間隙X=0.061mm。
因而尺寸(15±0.25)mm能夠保證。
(3)φ10H9軸線對φ25H7軸線的平行度0.3mm的精度校核。
ΔD=0. 03mm,ΔA=0. 03mm。
襯套對底面(F)的垂直度誤差ΔT=0. 05mm。
因而此夾具能保證兩孔軸線的平行度要求。
7.繪制夾具總圖
根據(jù)已完成的夾具結構草圖,進一步修改結構,完善視圖后,繪制正式夾具總裝圖,如圖2-2-23所示。
8.繪制夾具零件圖樣
從略。
9.編寫設計說明書
從略。
銑床夾具設計實例
圖2-2-25所示為軸套類零件的零件圖樣?,F(xiàn)需設計銑兩槽5 mm的銑夾具。
1.零件本工序的加工要求分析
本工序的加工要求,在實體上銑出兩通槽,槽寬為5 mm,槽深為27 mm,兩槽在圓周方向互成60°±30′角度,表面粗糙度為Ra1. 25μm。
本工序之前,外圓φ60 mm、內孔φ32 mm及兩端面均已加工完畢。
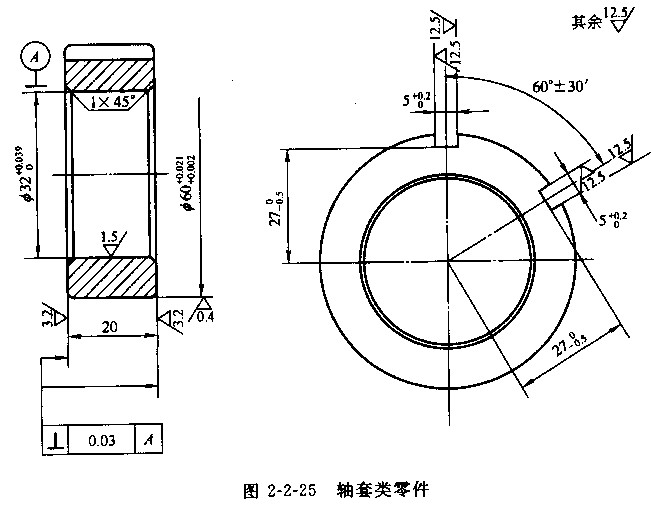
本工序采用φ5mm標準鍵槽銑刀在X5l立式銑床上,一次裝夾六件進行加工。
2.確定夾具類型
本工序所加工的是兩條在圓周互成60°角的縱向槽,因此宜采用直線進給帶分度裝置的銑夾具。
3.擬定定位方案和選擇定位元件
(1)定位方案。
①以φ32 mm內孔作為定位基準,再選孔端面為定位基準,限制工件五個自由度。如圖2-2-26(a)所示。
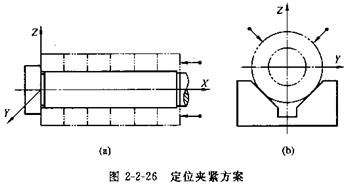
②以φ60 mm外圓為定位基準 (以長V形塊為定位元件),限制4個自由度。如圖2-2-26 (b)所示。
方案②由于V形塊的特性,所以較易保證槽的對稱度要求,但對于實現(xiàn)多件夾緊和分度較困難。
方案①的不足之處是由于心軸與孔之間有間隙、不易保證槽的對稱度,且有過定位現(xiàn)象。但本工序加工要求井不高,而工件孔和兩端面垂直精度又較高,故過定位現(xiàn)象影響不大。
經(jīng)上述分析比較,確定采用方案①。
(2)選擇定位元件。根據(jù)定位方式,采用帶臺肩的心軸。心軸安裝工件部分的直徑為φ32g6( )mm,考慮同時安裝6個工件,所以這部分長度取112mm,由于分度精度不高,為簡化結構,在心軸上做出六方頭,其相對兩面間的距離尺寸取28g6( )mm,與固定在支座上的卡塊槽28H7( )mm相配合;加工完畢一個槽后,松開并取下心軸,轉過相鄰的一面再嵌入卡塊槽內即實現(xiàn)分度。心軸通過兩端φ25H6mm柱部分安裝在支座的V形槽上,并通過M16螺栓鉤形壓板及錐面壓緊,壓緊力的方向與心軸軸線成45°角。
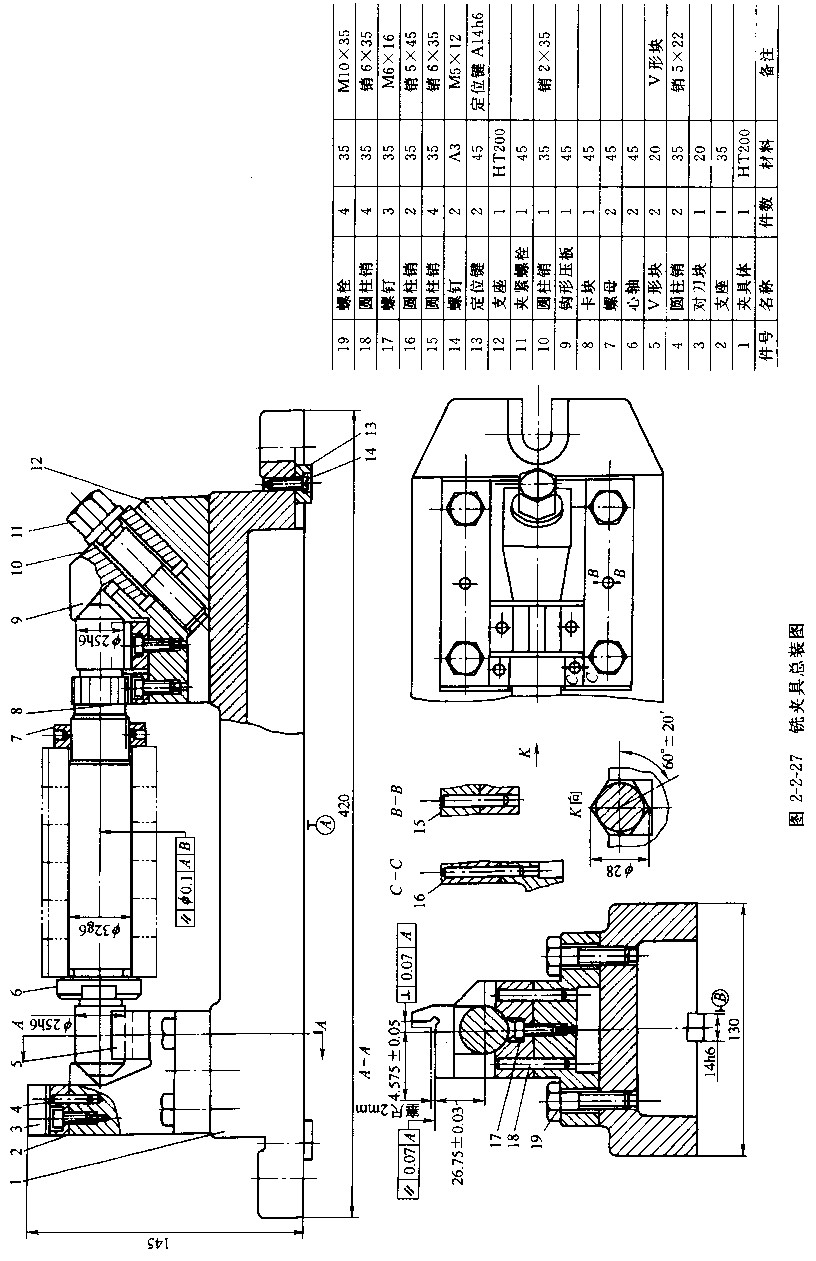
(3)定位誤差計算。工序尺寸27 mm 定位誤差分析如下。
由于基準重合ΔB=0
由于定位孔與心軸為任意邊接觸,則因此定位精度足夠。
由于加工要求不高,其他精度可不必計算。
4.確定夾緊方案
根據(jù)圖2-2-26所示心軸結構,用M30螺母把工件軸向夾緊在心軸上。心軸的具體結構如圖2-2-27所示。
5.確定對刀裝置
(1)根據(jù)加工要求,采用GB/T2242-80直角對刀塊;塞尺符合GB/T2244-80,基本尺寸及偏差2 mm。
(2)計算對刀尺寸H和B
如圖2-2-28所示,計算時應把尺寸化為雙向對稱偏差,即
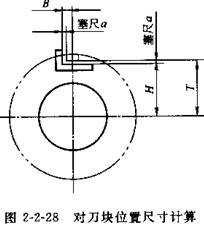
6.夾具精度分析和計算
本夾具總圖上與工件加工精度直接有關的技術要求如下。
定位心軸表面尺寸φ32g6。
定位件與對刀間的位置尺寸(24.75±0.08)mm,(4.575±0.05)mm。
定位心軸安裝表面尺寸φ25h6。
對刀塞尺厚度尺寸2 mm。
分度角度60°±10′。
定位心軸軸線與夾具安裝面、定位鍵側平面間的平行度公差為0. lmm。
分度裝置工作表面對定位表面的對稱度公差為0. 07mm。
分度裝置工作表面對夾具安裝面垂直度公差為0.07mm。
對刀裝置工作表面對夾具安裝面的平行度和垂直度公差為0. 07mm。
(1)尺寸27 mm的精度分析。
ΔD=0. 064mm(定位誤差前已計算)。
ΔT=0. 16mm(定位件至對刀塊間的尺寸公差)。
ΔA= ×20mm=0.0086mm(定位心軸軸線與夾具底面平行度公差對工件尺寸的影響)。
故此夾具能保證27 mm尺寸。
(2)對60°±30′的精度分析。
分度裝置的轉角誤差可按下式計算。
故此分度裝置能滿足加工精度要求。
7.繪制夾具總圖
圖2-2-27所示為本夾具的總裝圖樣。
8.繪制夾具零件圖樣
從略。
9.編寫設計說明書
從略。
夾具設計實例信息由思誠資源網(wǎng)提供,有需要請點擊EROWA夾具